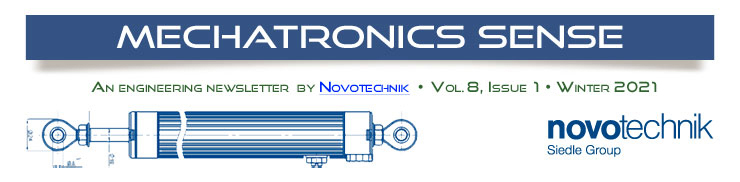 |
In this issue:
• Virtual Reality Technology Aids Patients With Trauma and Other Conditions
• Tech Tip: Much faster injection molding
• Application: Hay Baler lift, rotation and tilt controls
• and more.
To view newsletter in your browser click here.
Featured video: Click here.
|
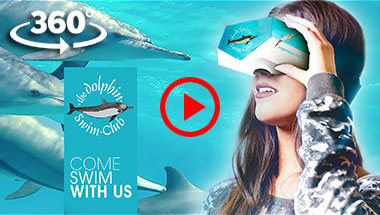
After linking to site, scroll down to run interactive video. |
|
|
 Virtual Reality Technology Aids Patients With Trauma and Other Conditions |
While not everyone has tried a virtual reality (VR) device, almost everyone has heard of them. This technology can make the user feel like the images they are seeing are real, that they are immersed in what they are viewing.
While the main application VR manufacturers have found a market for is the gaming market, there are other more serious applications. These include medical and safety. One safety application, according to a VR headset manufacturer is training for mining rescue teams. Another is training ER doctors for rapid response situations, without the consequences of treating a real patient.
The medical application described below combines several technologies to create an environment that can change someone's life for the better. Dr. Brennan Spiegel, Director Health Services Research at Cedars-Sinai Medical Center gave a lecture at the 2nd Virtual Medicine Conference in 2019. During that talk, Dr. Spiegel said, "that therapeutic VR can manipulate sensations and those sensations can generate emotions in the body and feelings in the brain and ultimately cognitions (feelings of knowing)...VR is a tool that modifies perception."
Marijke Sjollema and Benno Brada are not doctors but they have a vision to help people by combining VR technology and dolphins. Dr. Speigel references their organization in his talk. Using six Gopro video cameras packed in a waterproof case called Kolor Rig and some special software called Kolor Autopano, Marijke and Benno were able to pu together an amazing interactive video that is used with the Oculus Go 64GB VR headset to create a 360° VR experience that has helped people. They and their team captured everything with 6k resolution, added 40 man-hours of post production processing and combined natural captured spinner dolphin sound plus special music with the video. Together, they designed an effective treatment for many patients.
Their creation is used by medical treatment platforms including AppliedVR, Psious and SyncVR.
Sources:
See the interactive 3D video.
Dr. Speigel's lecture
|
|
|

|
Faster Injection Molding - Lifting The Speed Limits of Technology |
I |
|
n general, injection molding machine customers are concerned about the speed at which they can process parts while maintaining a high level of quality with consistencyamongst other things. |
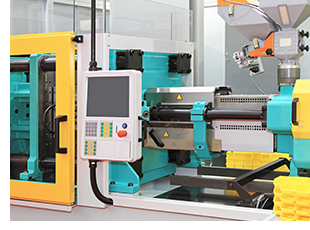 |
Injection molding machine manufacturers know their customers value reliability, quality and throughput. After all when a company invests in a piece of capital equipment for manufacturing, the faster the throughput of quality parts from that machine, the more that machine looks like a good investment.
Current injection molding machine manufacturers use technologies like closed-loop control to maintain quality when facing variations in resin viscosity from shot to shot.
|
They need to avoid undershoot where the mold is not completely filled as well as overshoot which can cause flashresin flowing out beyond the mold cavity where the mold halves meet.
Current machine technology is pushing to and past 800 mm/sec (31.5 in/sec). This means the speed that the position of the rods is delivered to a controller and the precision of that position value are critical in achieving the goals mentioned above. The trick is to very accurately control the speed, stopping point and time-to-stop from shot to shot. Especially enabling a higher speed, then decelerating extremely quickly for the shortest stopping distance. To achieve this level of control portions of motion during this process have to be monitored at a much faster rate than the screw is traveling to push resin into the mold.
Closed loop control systems can apply information to make very minute adjustments for each shot based on information from the previous shot if it is available to the controller soon enough.
It turns out that "soon enough" means taking position measurements that are accurate to < 1mm while moving at a high rate of speed and < 0.1 mm positioning precision at low speed. This position needs to be acquired between every 0.05 and 0.20 msec while delivering that position information to the controller in 0.25 msec.
These time values translate to having position sensors that are capable of sample rate of 0.1 msec and propagate the signal from the mechanical input to the signal output significantly less than 0.5 msec so that the controller has time to update the information to the hydraulic controls that move the screw and open/close the mold.
But there's a problem. Magnetostrictive technology can only acquire position information at a theoretical sample rate of about 0.2 to 0.25 msec. The physics of it reveals the echos, from the magnetic marker, can only travel so fast to the sensor. Current magnetostrictive devices also have a sample rate of 0.25 to 0.5 msec or longer. The way injection molding machine manufacturers are getting past this problem is to use advanced inductive technology position sensors. Instead of moving a magnet, they move an epoxy-sealed, precision inductive marker along the position sensor length. The result is sensors that are able to deliver about 1μm of precision to the output for the controller to read in 0.25 msec. And the rate of operation is between 10 and 15 kHz.
Some of the benefits and features of advanced inductive technology sensors are:
- Not Magneticavoid errors from magnetized metal flakes or filings. TF1 Series'
technology does not incorporate a magnet in the moving position marker that can trap
flakes between the marker and sensor.
- EMI Immunityour advanced inductive sensing is immune to spurious errors from
electro-magnetic interference (EMI) generated by high-powered machinery.
- Speedwith an update rate of 100 μsec, it is much faster than virtually any
magnetostrictive sensor, and it maintains its full accuracy up to its 10 kHz cycle rate.
- RobustTF1 Series of sensors maintain critical specifications, including absolute
linearity of ≤ ± 0.025%, while operatingeven when subjected to their specified 20 g of
vibration and 100 g shock. Many magnetostrictive sensors do not come close.
Here's an in-depth look at one of these advanced inductive sensors and its unique capabilities and advantages. |
|
|
|
Hay Baler lift, rotation and tilt controls |
|
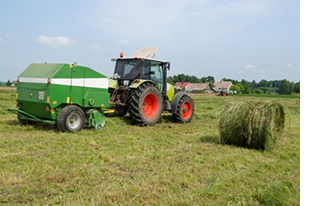
|
A lager farm equipment manufacturer needed a better sensor to improve sealing, enable smoother hydraulic control and have an output suited for mobile applications on a hay baler. Novotechnik's RFC4800 Series of angle sensors met their needs for controlling the bale fork lift as well as turntable rotation and tilt. Because the technology is touchless magnetic, the sensor is encapsulated, sealing it and separate from the moving the various moving parts of the vehicle that required position tracking. Click here for more information on the RFC 4800 Series sensor product used in this application.
|
|
|
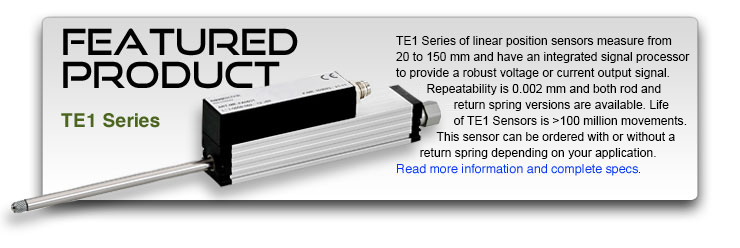 |
Please email suggestions for technical subjects you would like to suggest for this newsletter to this link: Newsletter Editor
|
|